Laser cutting is a precise and efficient method used in various industries to cut and shape materials. This process involves utilizing a high-energy beam from a laser to melt, burn, or vaporize the material, resulting in a clean and accurate cut. A crucial component in this process is the use of assist gases, particularly nitrogen, to ensure quality and efficiency.
Nitrogen plays a significant role across various sectors, including metal fabrication, automotive, aerospace, and electronics. In the food industry, this gas helps preserve the freshness of products by reducing oxidation. When it comes to nitrogen generator for laser cutting, systems that provide a continuous and reliable supply of high-purity gas are essential for optimal performance.
The Role of Nitrogen in Laser Cutting
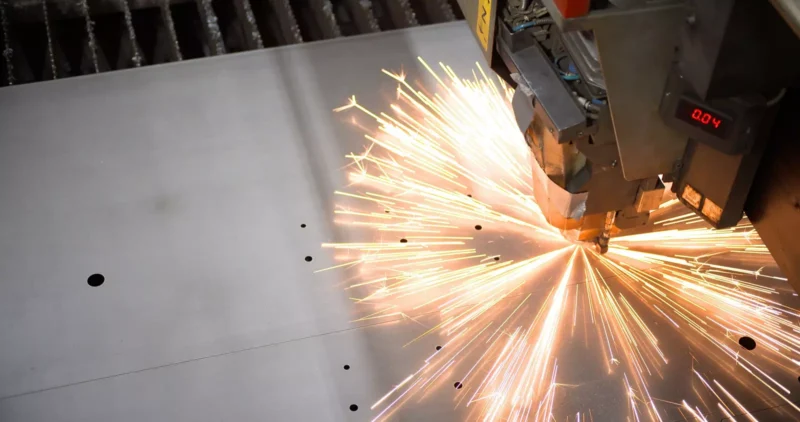
This inert gas acts as a shielding agent during the laser-cutting process. It is used to blow away molten material from the cut zone, preventing oxidation and ensuring a clean edge, especially for metals like stainless steel and aluminum. Maintaining an oxygen-free environment is crucial for the integrity and appearance of the cut material.
Using this gas in laser cutting also helps achieve faster speeds and better efficiency. By focusing the laser energy solely on cutting, unwanted chemical reactions are minimized, resulting in smoother and more precise cuts and reducing the need for additional finishing processes.
How Nitrogen Systems Work
These systems produce gas by separating it from the surrounding air. The air we breathe consists of about 78% nitrogen, 21% oxygen, and trace amounts of other gases. Advanced technologies isolate specific molecules from the air, delivering high-purity gas for industrial applications, including laser cutting.
Types of Nitrogen Systems
There are two primary types of systems used in laser cutting: Pressure Swing Adsorption (PSA) and Membrane Systems. Each employs a different method to extract the required gas from the air.
- Pressure Swing Adsorption (PSA) Systems: PSA systems operate on the principle of adsorption. Ambient air is compressed and passed through a vessel containing adsorbent materials, typically carbon molecular sieves (CMS), which selectively adsorb oxygen and other impurities, allowing the desired gas to pass through. The process repeats, ensuring a continuous supply.
- Membrane Systems: Membrane systems use hollow fiber membranes to separate gases. Compressed air is forced through these membranes, which have selective permeability. Oxygen and other gases permeate through the membrane walls, while the required gas is retained and collected as the product. These systems are known for simplicity, reliability, and low maintenance.
Advantages of Using Nitrogen Systems in Laser Cutting
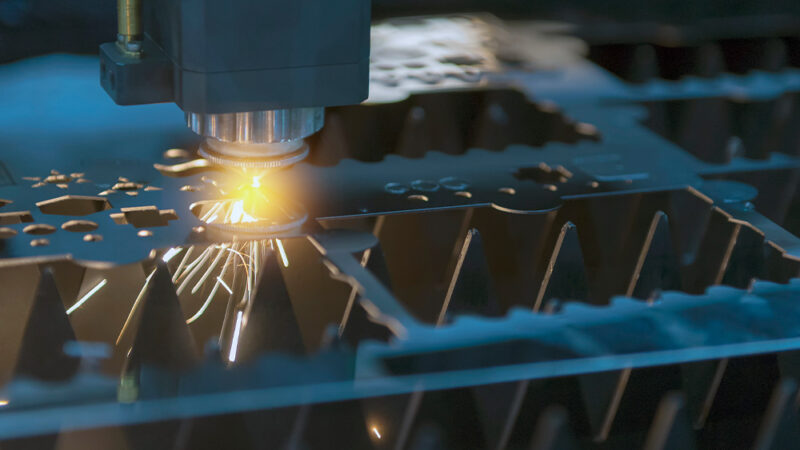
On-site production eliminates the need to purchase and transport bottled gas, reducing operational costs and logistical challenges. These systems provide a reliable supply, ensuring uninterrupted laser cutting operations.
High-purity gas is essential for achieving clean and precise cuts without oxidation. On-site production also reduces the carbon footprint associated with transporting and storing gas cylinders. Additionally, systems can be tailored to meet specific purity and flow rate requirements, enhancing flexibility and efficiency.
Applications Beyond Laser Cutting
While these systems are integral to laser cutting, their applications extend to various other industries. In the food industry, they are used to create modified atmosphere packaging (MAP), which extends the shelf life of perishable products. The technology helps maintain product freshness by displacing oxygen and inhibiting the growth of aerobic bacteria.
In the electronics industry, these systems are used for soldering and wave soldering processes. The presence of an inert gas helps create an atmosphere that prevents oxidation, ensuring high-quality solder joints. In the pharmaceutical industry, it is used for packaging and preserving sensitive products, ensuring their stability and shelf life.
Maintenance and Operation of Nitrogen Production Systems
Proper maintenance and operation are crucial for ensuring optimal performance and longevity. Regular inspections, filter replacements, and adherence to manufacturer guidelines are essential. Additionally, monitoring purity levels and system pressure helps maintain consistent quality and efficiency.
Operators should be trained to handle the equipment properly and to recognize signs of wear or malfunction. Regular servicing by qualified technicians can prevent unexpected downtime and costly repairs. Keeping detailed records of maintenance activities and performance metrics can also help in identifying trends and making informed decisions about equipment upgrades or replacements.
Technological Advancements in Nitrogen Production

Technological advancements have significantly improved the efficiency and functionality of these systems. Modern units are equipped with sophisticated monitoring and control features that enhance their reliability and performance. For example, some now come with remote monitoring capabilities, allowing operators to track performance and receive alerts about potential issues from anywhere.
Energy efficiency has also been a focus of recent developments. Newer systems are designed to consume less energy, making them more cost-effective and environmentally friendly. These advancements not only reduce operational costs but also contribute to sustainability goals.
Implementing Nitrogen Production Systems in Laser Cutting Operations
Integrating these systems into laser cutting operations requires careful planning and consideration. It’s essential to assess the specific needs of the operation, including the required purity, flow rate, and pressure. Working with a reputable supplier can help ensure that the chosen system meets these requirements and is compatible with existing equipment.
Proper installation and setup are critical for achieving optimal performance. This may involve customizing the system to match the unique specifications of the laser cutting operation. Once installed, regular training and support from the supplier can help operators maximize the benefits of the system.
Future Trends in Nitrogen Generation
The future of gas generation looks promising, with ongoing research and development aimed at further enhancing the technology. One emerging trend is the integration of artificial intelligence (AI) and machine learning to optimize the operation and maintenance of these systems. AI can predict maintenance needs, optimize energy consumption, and ensure consistent purity, thereby improving overall efficiency.
Another trend is the development of more compact and portable systems. These units are designed to be easily transported and set up in various locations, providing flexibility for operations that require on-site gas generation in different areas.
Conclusion
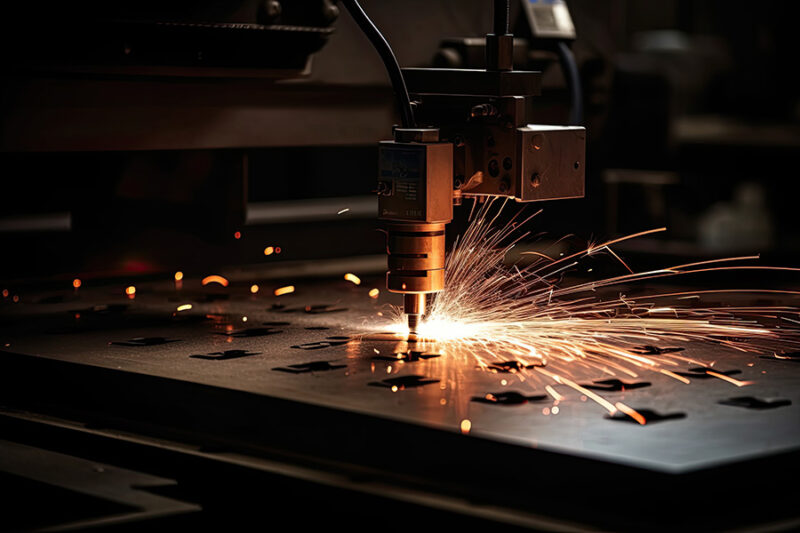
Nitrogen production systems play a pivotal role in the laser cutting process, providing a continuous supply of high-purity gas that ensures clean, precise, and oxidation-free cuts. The technology behind these systems, whether PSA or membrane-based, offers cost-effective, reliable, and environmentally friendly solutions for various industrial applications. By understanding how these systems work and their benefits, industries can enhance their cutting processes and achieve superior results.
In addition to laser cutting, these systems have broad applications in industries such as food packaging, electronics, and pharmaceuticals. Their ability to provide high-purity gas on-demand makes them an invaluable asset for maintaining product quality and operational efficiency. Proper maintenance and operation are key to maximizing the lifespan and performance of these systems, ensuring a consistent supply for all industrial needs.
Technological advancements continue to drive the evolution of gas generation, with innovations in energy efficiency, remote monitoring, and AI integration. As these technologies advance, production systems will become even more efficient and versatile, supporting a wide range of industrial applications. By staying informed about these developments and implementing best practices for maintenance and operation, businesses can fully leverage the benefits of these systems in their operations.