Automation has become a cornerstone for efficiency and productivity in today’s industrial landscape, with Cobots and Industrial Robots emerging as frontrunners in this realm. This article delves into the nuances of Cobots and Industrial Robots, shedding light on their differences and applications.
Cobots, short for collaborative robots, are designed to work alongside humans in a shared workspace, facilitating interaction and cooperation. In contrast, Industrial Robots are typically large, standalone machines programmed to perform tasks autonomously, often in segregated environments.
Understanding the disparities between these two technologies is crucial for industries seeking to implement automation solutions effectively.
Understanding Cobots
Cobots represent a new era in robotics, characterized by their collaborative nature. Equipped with advanced sensors and safety features, Cobots can detect and respond to the presence of humans in their vicinity, ensuring a safe working environment.
These robots find applications across various industries, including manufacturing, healthcare, logistics, and agriculture, where they streamline processes and improve efficiency while minimizing the risk of accidents.
Understanding Industrial Robots
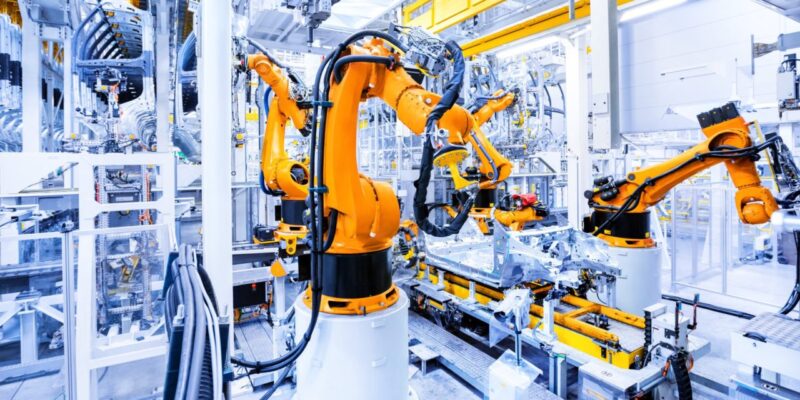
Industrial Robots, in contrast to Cobots, are synonymous with traditional automation. With high payload capacities and precise control mechanisms, Industrial Robots excel in applications requiring speed, accuracy, and endurance.
Industries such as automotive manufacturing, electronics production, construction, and food processing heavily rely on Industrial Robots to streamline production processes and achieve consistent quality standards.
In particular, car manufacturing robots play a crucial role in automotive assembly lines, where they perform tasks such as welding, painting, and assembly with remarkable precision and efficiency.
Critical Differences Between Cobots and Industrial Robots
Cobots are designed to collaborate with human workers, sharing workspace and tasks seamlessly. In contrast, Industrial Robots operate in isolation, performing tasks independently without human intervention.
They are equipped with advanced safety features, such as force-limiting sensors and hand-guiding capabilities, to ensure safe human-robot interaction. Industrial Robots adhere to stringent safety regulations but rely more on physical barriers and safety zones to prevent accidents. They excel in flexibility and adaptability thanks to their modular design and intuitive programming interfaces. These robots can be easily reprogrammed and redeployed to perform a wide range of tasks, making them ideal for environments with changing production needs.
Industrial Robots, while versatile in their own right, often require more complex programming and setup, limiting their flexibility to some extent.
Cobots typically have a lower upfront cost compared to Industrial Robots, making them more accessible to small and medium-sized enterprises. Additionally, Cobots require less infrastructure and safety measures, further reducing overall implementation costs.
They are designed with user-friendly interfaces and intuitive programming languages, allowing operators with minimal technical expertise to program and deploy them quickly. Industrial Robots, on the other hand, often require specialized training and expertise to program and integrate into existing workflows, adding to the implementation timeline and costs.
Comparative Analysis ─ Strengths and Weaknesses
Advantages of Cobots
- Enhanced collaboration ─ Cobots can work alongside human operators, leveraging their strengths and capabilities to improve productivity and efficiency.
- Increased flexibility ─ Cobots are easily reprogrammable and adaptable to changing production needs, enabling agile manufacturing processes.
- Improved safety ─ With built-in safety features and sensors, Cobots minimize the risk of accidents and injuries in the workplace.
Advantages of Industrial Robots
- Higher payload capacities ─ Industrial robots are capable of handling heavier loads and performing tasks that require significant strength and endurance.
- Speed and precision ─ Industrial robots excel in tasks that demand high-speed operation and precise control, ensuring consistent quality and output.
- Scalability for large-scale operations ─ In industries with high-volume production requirements, Industrial Robots offer scalability and efficiency, enabling mass production on a large scale.
Limitations and Challenges
- Cobots ─ Limited payload capacities and slower operation speeds compared to Industrial Robots may restrict their applicability in specific industries and tasks.
- Industrial robots ─ Complex programming requirements and the need for specialized expertise may pose challenges for small and medium-sized enterprises looking to implement automation solutions.
Choosing the Right Solution ─ Factors to Consider
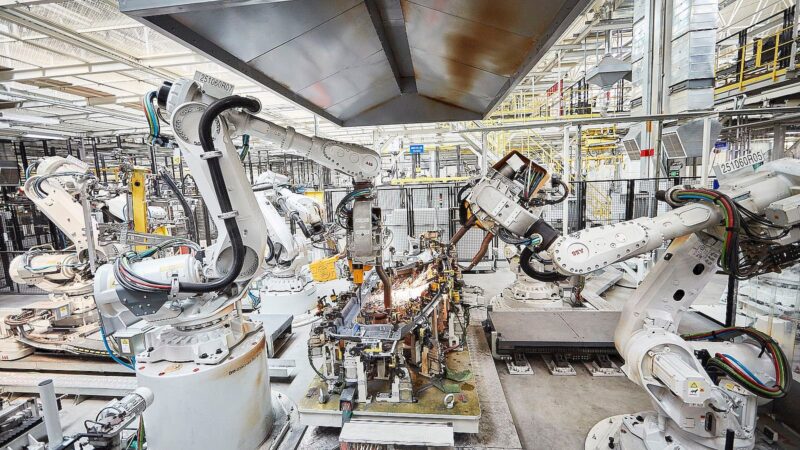
When selecting between Cobots and Industrial Robots, several factors should be taken into account:
- Work environment and tasks ─ Assess the specific requirements of the intended application, including payload capacities, speed, precision, and safety considerations.
- Safety requirements ─ Evaluate the safety standards and regulations governing the industry and ensure that the chosen solution complies with them.
- Budget and ROI analysis ─ Conduct a thorough cost-benefit analysis to determine the long-term return on investment and affordability of the chosen automation solution.
- Future scalability and integration needs ─ Consider the scalability of the chosen solution and its compatibility with existing systems and workflows to accommodate future growth and expansion.
Conclusion
The comparison between Cobots and Industrial Robots underscores the importance of understanding the unique characteristics and functionalities of each technology. By carefully evaluating factors such as safety, scalability, and cost, industries can choose the right automation solution to meet their specific needs and achieve their production goals.
As automation continues to reshape industries worldwide, the synergy between humans and robots will pave the way for a future of innovation and efficiency in manufacturing and beyond.
Related Posts:
- Manufacturer vs. Wholesaler: Understanding the Key…
- 24 Peculiar Differences Between A Online Meeting vs Webinar
- LED Neon vs Glass Neon Signs: Major Differences
- Intel VS AMD? - CPU Differences & Similarities in Gaming
- Differences Between Atlantic City and Las Vegas - 2024 Guide
- What are the Differences Between Social and…