Metal fabrication is essential in industries ranging from construction and engineering to automotive and product design. Whether you need custom components, structural elements, or decorative metalwork, metal sheet fabrication provides the precision and durability required for a wide range of applications. Skilled fabrication ensures the structural integrity of components, supporting safety and functionality. Advanced technology and industry expertise improve efficiency and product longevity.
Key Points:
- Metal sheet fabrication includes cutting, bending, welding, and finishing processes.
- Choosing the right service depends on material expertise, customization, and quality control.
- Industries like construction, automotive, and aerospace rely on metal fabrication for critical components.
- Lead times, efficiency, and precision play a key role in selecting a provider.
- High-quality fabrication improves durability, fit, and long-term performance.
What Is Metal Sheet Fabrication?
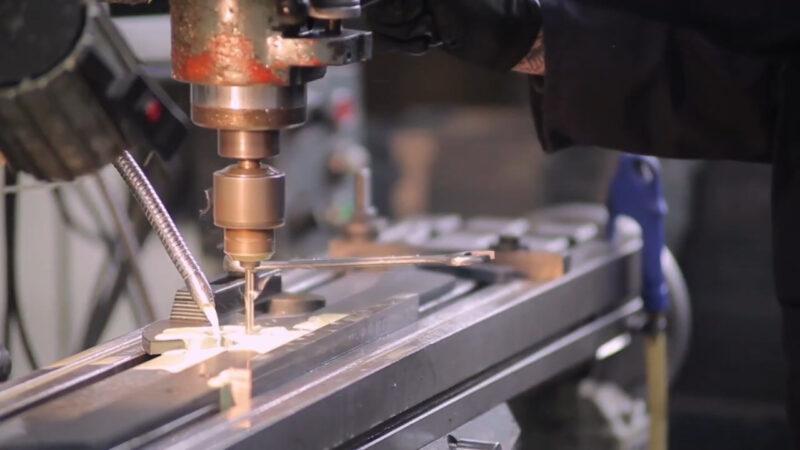
Metal sheet fabrication is the process of cutting, bending, and assembling metal sheets into finished products or components. This technique is used to create everything from machinery parts to architectural features, ensuring strength, accuracy, and consistency in production.
The process typically includes:
- Cutting – Using laser cutting, plasma cutting, or waterjet cutting for precise shapes.
- Bending – Forming metal sheets into specific angles and curves.
- Welding – Assembling and joining metal parts securely.
- Finishing – Applying coatings, polishing, or treating the surface for durability and appearance.
Choosing the Right Metal Sheet Fabrication Service
When searching for metal sheet fabrication near you, consider these key factors:
- Material Expertise – Different metals require different fabrication techniques. Ensure the provider works with the specific material you need, whether it’s stainless steel, aluminum, or mild steel.
- Customisation and Capabilities – Some projects require complex designs or unique specifications. Look for a service that offers custom fabrication tailored to your requirements.
- Precision and Quality Control – High-quality fabrication ensures durability and proper fit. Check if the company follows strict quality control processes.
- Lead Times and Efficiency – Fast turnaround times are crucial for meeting project deadlines. Ask about production schedules and delivery options.
Industries That Rely on Metal Sheet Fabrication
Metal sheet fabrication plays a critical role in multiple industries, providing durable, custom-engineered components for various applications. The precision and versatility of fabricated metal parts make them indispensable in fields that demand strength, efficiency, and accuracy.
Construction Industry
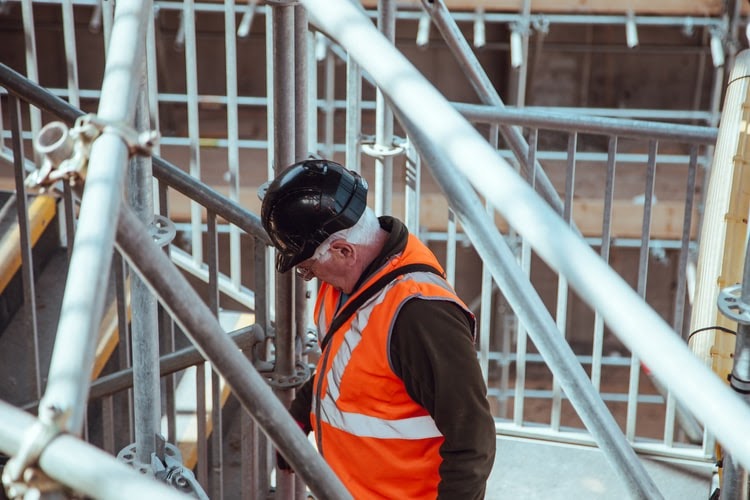
Buildings, bridges, and infrastructure projects depend on metal fabrication for strength and longevity. Structural frameworks, wall panels, support beams, and roofing materials are all made using precision-cut metal sheets. Fabricated metal components withstand harsh environmental conditions, ensuring safety and durability in construction projects.
Automotive
Vehicle manufacturing requires high-quality metal components to enhance durability, aerodynamics, and crash resistance. Metal sheet manufacturing is used for car body panels, engine parts, and reinforcements. Precision cutting ensures parts meet strict industry standards, improving fuel efficiency and vehicle performance.
Manufacturing Industry
Metal fabrication is essential for producing industrial machinery, storage enclosures, and specialized equipment. Factories rely on custom-fabricated metal parts for conveyors, assembly lines, and automated systems. The ability to create precise, high-tolerance parts makes metal manufacturing a key component of modern manufacturing.
Aerospace Industry
Aircraft and space technology demand advanced metal manufacturing for critical parts. Aluminum, titanium, and stainless steel sheets are used for fuselages, turbine blades, and structural reinforcements. Precision metal fabrication ensures components meet strict weight and strength requirements, supporting safety and efficiency in aerospace applications.
Key Considerations for Custom Fabrication
For custom metal fabrication, attention to detail ensures accuracy and performance. The following factors affect the outcome of any custom fabrication project:
- Design Complexity – The complexity of the design determines fabrication time and cost.
- Material Choice – Different metals react differently under stress and environmental exposure.
- Tolerances and Precision – High-tolerance projects require advanced machinery and expertise.
- Finishing Techniques – Powder coating, galvanizing, or anodizing enhance longevity and appearance.
- Budget and Production Volume – Costs vary depending on the volume and level of customization.
Advantages of Working with an Experienced Fabricator
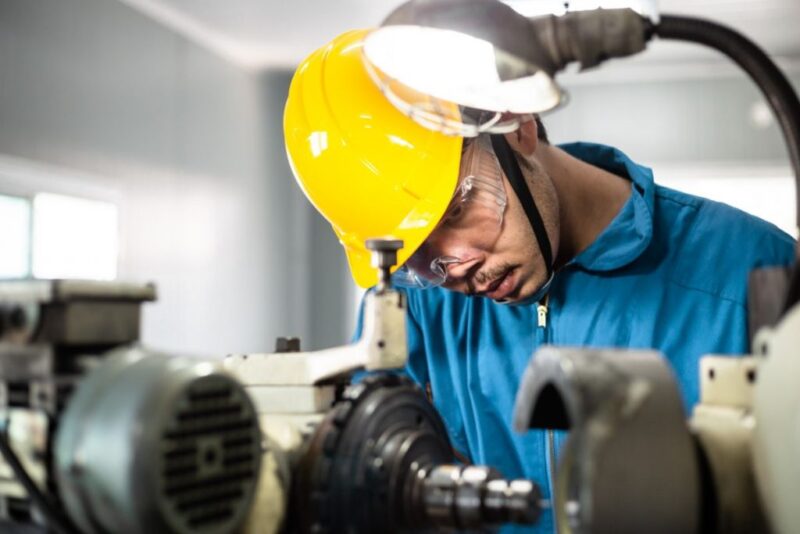
Choosing an experienced provider brings several advantages.
Technical Expertise
Skilled professionals ensure precise execution, reducing material waste and production errors. Their expertise allows for better structural integrity and high-quality finishes.
Advanced Equipment
State-of-the-art machinery produces high-quality results, improving efficiency and accuracy. Modern fabrication tools enable complex designs that meet strict tolerances.
Efficient Project Management
Experienced fabricators streamline production schedules, ensuring timely completion of projects. Effective coordination reduces downtime and enhances workflow.
Compliance with Regulations
Industry standards and safety regulations are strictly followed, ensuring fabricated components meet required certifications. Compliance reduces risks and enhances reliability.
Reliable Customer Support
Assistance with design modifications and troubleshooting helps clients achieve their desired results. Ongoing support ensures projects run smoothly from start to finish.
The Role of Fabrication in Sustainable Manufacturing
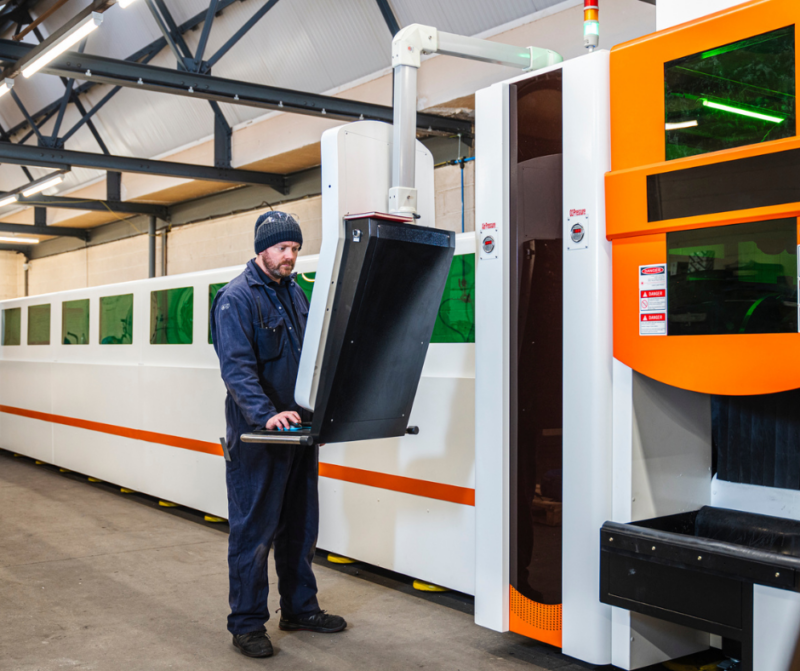
Sustainability in metal fabrication focuses on reducing waste, improving energy efficiency, and using eco-friendly materials. Many companies incorporate recycling processes to minimize scrap metal and optimize production methods. Advanced manufacturing techniques, such as laser cutting and robotic automation, help reduce environmental impact while maintaining high precision. Investing in sustainable practices enhances long-term profitability and aligns with global efforts to minimize industrial waste.
Common Mistakes to Avoid in Metal Fabrication Projects
Mistakes in manufacturing lead to costly delays and material waste. Avoid the following errors:
- Inaccurate Measurements – Even slight miscalculations can lead to improper fits.
- Ignoring Material Properties – Selecting the wrong metal affects durability and performance.
- Neglecting Quality Control – Skipping inspections leads to defects.
- Poor Welding Practices – Weak welds compromise structural integrity.
- Overlooking Coating Needs – Failing to apply protective coatings results in corrosion.
Finding the Best Fabrication Partner
Whether you need large-scale production or a one-off custom piece, choosing a reputable metal sheet fabrication provider ensures quality, precision, and reliability. By focusing on experience, material capabilities, and production efficiency, you can find the right service for your needs. Industry certifications, customer reviews, and past projects offer insight into a provider’s reliability. Ensuring strong communication and project transparency builds long-term trust between clients and fabricators.
Related Posts:
- Mastering Sheet Metal Cutting: Tips and Techniques…
- Why Video Quality of Streaming Services Look Better…
- Finding It Hard to Gain Weight? Here’s What You Can…
- Finding the Sweet Spot: How Much Should You Really Vape?
- 9 Tips For Finding A Reliable Assisted Living Facility
- 5 Tips For Finding the Right Gambling Game For You in 2024