Plastic moulding is at the heart of modern manufacturing, providing the components and products we use every day—from packaging and automotive parts to medical devices and consumer goods. In the UK, the plastic moulding industry has evolved into a hub of innovation, sustainability, and high-quality production, serving both domestic and international markets.
Local suppliers are building global reputations with competitive services and eco-aware practices.
Key Points:
- Plastic moulding shapes plastic into forms using moulds with different techniques.
- UK moulders follow strict quality and compliance standards.
- Local production shortens lead times and improves collaboration.
- Advanced technology enables complex and precise output.
- Sustainability is driving changes across the sector.
- UK suppliers offer resilience against global supply disruptions.
What is Plastic Moulding?
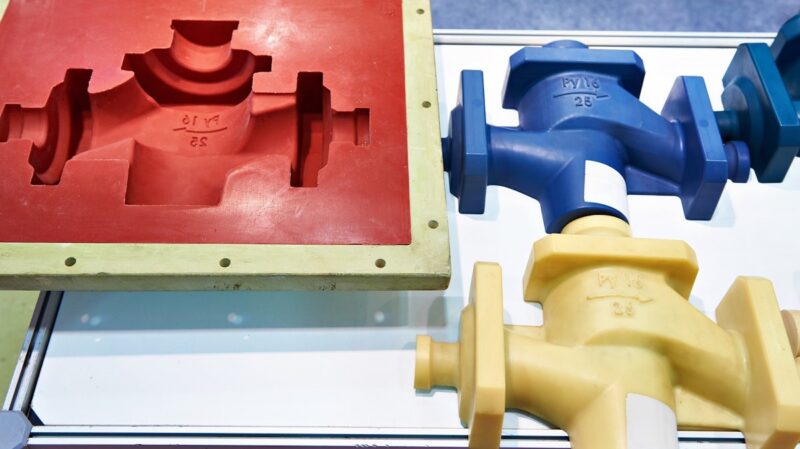
Plastic moulding is the process of shaping plastic materials into desired forms by using a mould. There are several types of plastic moulding processes, including:
- Injection Moulding: The most common method, where molten plastic is injected into a mould to create precise, repeatable components.
- Blow Moulding: Used for creating hollow products like bottles and containers.
- Rotational Moulding: Ideal for larger, hollow objects with uniform wall thickness.
- Thermoforming: Involves heating a plastic sheet and forming it over a mould.
Each method offers unique benefits depending on the product design, material requirements, and production volumes.
Why Choose a UK Plastic Moulding Supplier?
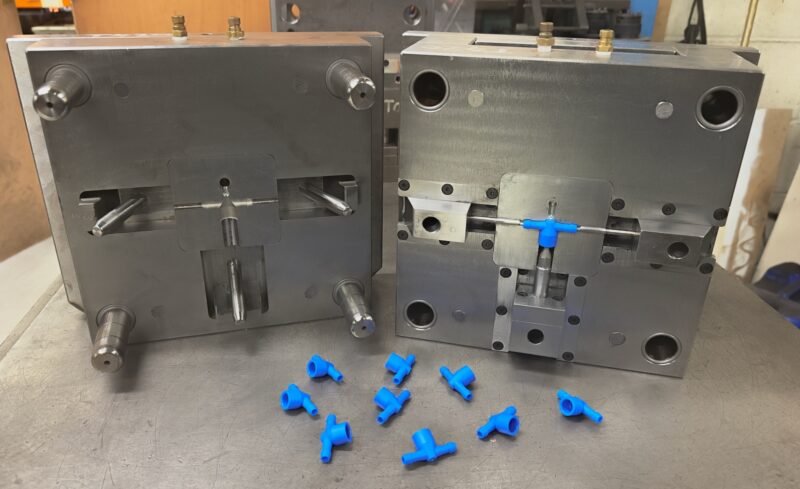
For businesses looking to manufacture plastic components, partnering with a UK-based plastic moulding company offers several advantages:
1. Quality and Compliance
UK plastic moulders operate under stringent quality management systems, often certified to ISO 9001, ISO 14001, or industry-specific standards. This ensures products meet high quality, safety, and regulatory requirements.
2. Shorter Lead Times and Local Support
Manufacturing locally reduces lead times, improves flexibility, and provides faster response to design changes or urgent orders. It also facilitates closer collaboration throughout product development.
3. Innovation and Technical Expertise
Many UK plastic moulders invest heavily in advanced tooling, CAD/CAM technology, and automation, enabling them to tackle complex projects and deliver high-precision components.
4. Sustainability Focus
With growing demand for sustainable solutions, UK plastic moulders are adopting recycled materials, biodegradable plastics, and energy-efficient processes to minimise environmental impact. Some companies even offer closed-loop recycling systems and material traceability.
5. Supply Chain Resilience
Recent global disruptions have highlighted the risks of relying solely on overseas suppliers. Working with a UK-based moulder strengthens supply chain resilience and reduces exposure to international shipping delays or tariffs.
Industries Served by UK Plastic Moulders
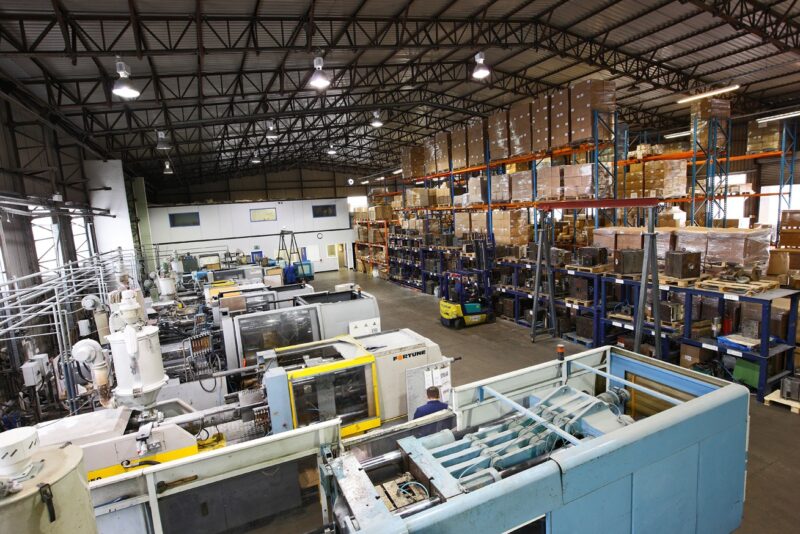
Plastic moulding plays a critical role across multiple industries in the UK, where precision, consistency, and scalability are essential. Companies rely on moulded components not just for cost-effective production, but also for meeting strict industry standards.
Key sectors include:
- Automotive and Aerospace: Plastic parts reduce weight without sacrificing durability. UK moulders produce housings, panels, and fluid system components that meet strict safety and performance criteria.
- Medical and Healthcare: From syringe bodies to surgical trays, plastic moulders supply cleanroom-manufactured, biocompatible parts that comply with MHRA or EU MDR regulations.
- Food Packaging and Containers: Safe, hygienic, and custom-formed packaging solutions are moulded for everything from meal trays to tamper-proof lids.
- Construction and Building Products: Items like electrical fittings, pipe connectors, and insulation accessories are mass-produced to meet building codes and safety standards.
- Electronics and Electrical Equipment: Casings, switchgear, and insulation parts are precision-moulded for consistency and performance.
- Consumer Goods and Retail Products: Toys, kitchen tools, and appliance components are designed for durability, branding, and cost-efficiency.
Many UK moulders do more than just manufacture parts. They often handle the full product lifecycle—design consultation, prototyping, mould tooling, volume production, quality control, and even final assembly and packaging—making them valuable long-term partners in product development.
Trends Shaping the UK Plastic Moulding Industry
The UK plastic moulding sector continues to evolve, driven by:
- Sustainability initiatives, including the use of recycled and bio-based plastics
- Lightweighting in automotive and aerospace components
- Increased demand for customisation and rapid prototyping
- Integration of Industry 4.0 technologies such as smart monitoring and automation
Companies that embrace these trends are better positioned to meet customer demands while reducing costs and environmental footprint.
Choosing the Right Plastic Moulding Partner
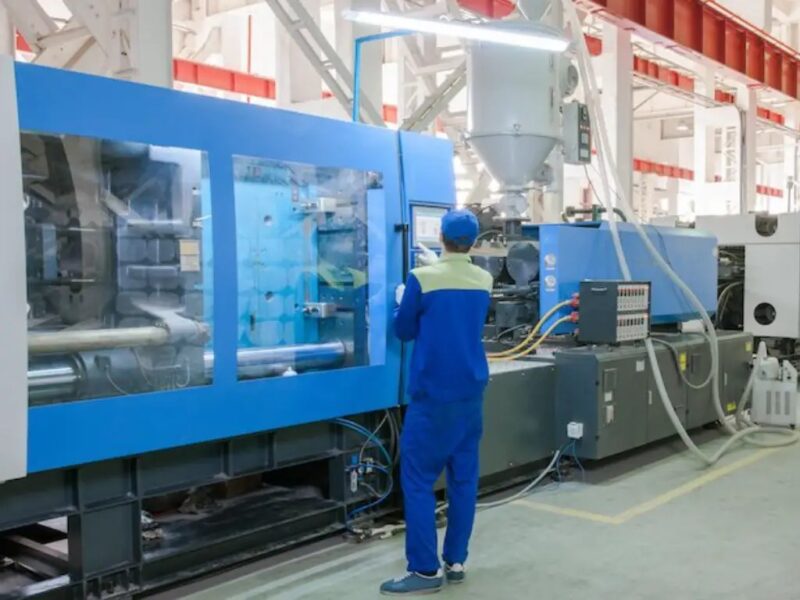
When selecting a plastic moulding company in the UK, consider factors such as:
- Technical expertise and capabilities
- Quality certifications and compliance
- Material options and sustainability practices
- Ability to scale production from prototype to high volume
- Customer support and project management
A good moulding partner doesn’t just manufacture parts—they collaborate with you to optimise design, reduce costs, and achieve the best possible outcome.
The Role of Prototyping in Modern Moulding
Prototyping plays a crucial role in bridging the gap between concept and production. Before committing to full-scale manufacturing, many UK moulders offer rapid prototyping services that help validate product designs and functions. This step reduces risk, minimises costs, and speeds up development timelines.
Benefits of integrating prototyping early:
- Identify design flaws before tooling.
- Evaluate multiple design iterations quickly.
- Test material suitability and tolerance limits.
- Gain stakeholder feedback before production.
- Shorten time-to-market with fewer revisions.
Clients who use prototyping gain better control over outcomes and cost planning. Prototypes can range from simple 3D prints to fully functional moulded parts using pilot tools.
Cost Drivers in Plastic Moulding Projects
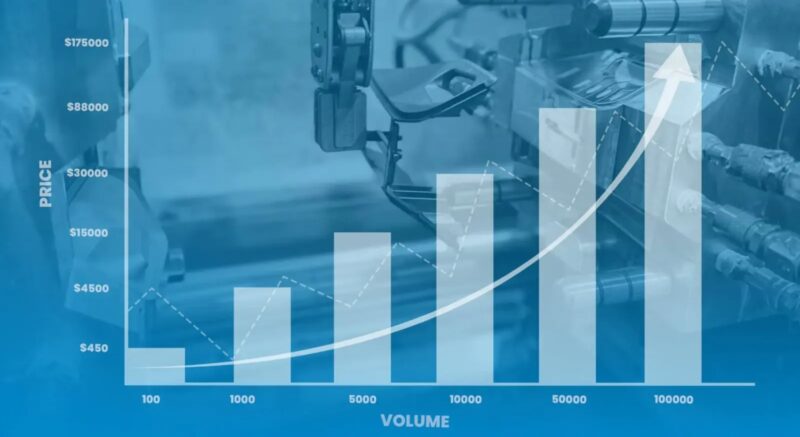
Several variables affect the final cost of a plastic moulding project. Understanding these cost drivers helps companies plan better and avoid unexpected charges. UK suppliers often provide transparent pricing and pre-production consultations to align budgets and project expectations.
Key factors influencing cost:
- Type of plastic and material availability.
- Mould complexity and cavity count.
- Production volume and cycle time.
- Required tolerances and finish levels.
- Post-moulding services like trimming, painting, or assembly.
Low-cost per part comes with higher volumes, but for niche or precision products, quality and reliability often justify a higher investment. UK moulders typically guide clients on optimal material choices to balance cost and performance.
Customisation for Industry-Specific Needs
Custom moulding allows businesses in regulated industries to meet strict design and compliance requirements. UK suppliers often specialise in tailoring solutions for sectors like medical, automotive, and defence. This involves specific material grades, certifications, and traceability features.
For example:
- Medical-grade plastics must be biocompatible and sterilisation-ready.
- Aerospace components require high strength-to-weight ratios and fire resistance.
- Consumer products demand safety compliance and aesthetic appeal.
Customisation goes beyond design. It includes packaging, logistics, and documentation adapted to industry standards. Working with a specialist moulder reduces approval risks and accelerates market entry.
Final Thoughts
Plastic moulding in the UK represents a blend of precision manufacturing, innovation, and environmental responsibility. Whether you’re a start-up launching a new product or an established company seeking a reliable production partner, UK plastic moulders offer the expertise and flexibility needed to succeed in today’s competitive markets.
If you’re considering outsourcing your plastic moulding needs, explore what UK manufacturers can deliver—and discover how local partnerships can drive your project forward